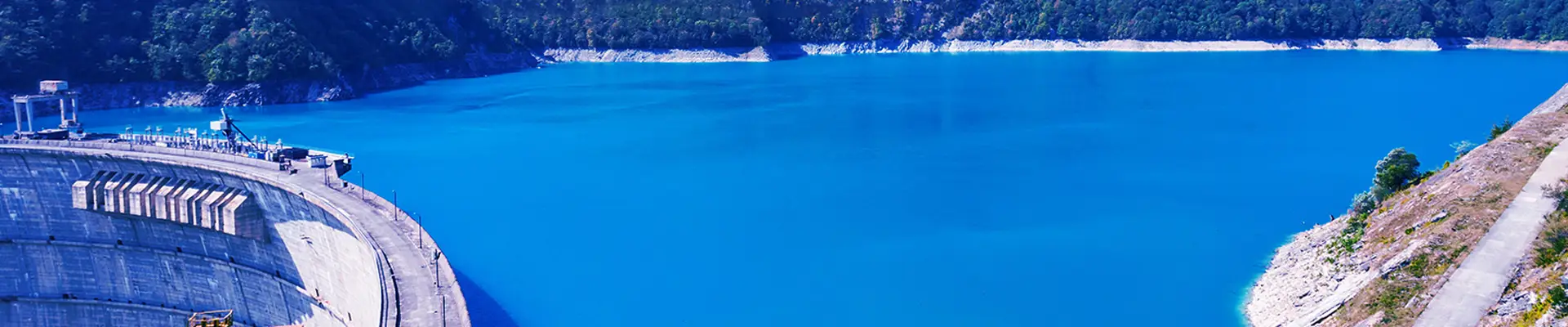





Food workshop polyurethane mortar floor
Classification:
Application Scenario
Key words:
Application Scenario
Product introduction
The material of the Tehl Polyurethane Mortar system is composed of a water-based polyurethane, isocyanate curing agent, a complex mortar, and a color pulp. The thickness of the polyurethane mortar system is generally 4-9mm. It is particularly suitable for places that require high chemical corrosion and cleanliness for heavy -duty workshops, food processing plants, beverage manufacturers, dairy factories, beer factories, beer factories, slaughter plants, laboratory, chemical factories, slurry and paper manufacturers.
Product advantage
Application field
Food processing: central kitchen, meat processing plant, milk processing plant, biscuits food processing, condiment factories, pickled product factories, washing rooms, slaughtering plants
Cold chain warehousing: ultra -low temperature, cold storage, meat frozen library, seafood freezer, supermarket store cold, repository
Wine and beverages: brewry, juice beverage factory, mineral water plant
Pharmaceutical: Pharmaceutical raw material workshop, Chinese medicine raw materials workshop, cleaning room, test factory
Packing and storage
◆ The place where it is cool, dry, and ventilated, stay away from the source of the fire, and store the appropriate temperature of 5 ° C -30 ° C.
◆ The preservation period of the original packaging is 6 months under normal storage conditions, of which the storage period of the part of the C (aggregate) is 3 months, and the harsh environment affects the storage time.
Construction process
Grassroots requirements
Project | indicator |
concrete grassroots | c25 or higher |
pressure resistance | 25MPa |
Lajan strength | 1.5MPa |
grassroots water content | < 8%(no bright water) |
Grassroots cleanliness | oil -free, dust, acid and alkali and old coatings |
Best construction temperature | 15-28 ℃ |
The above table is the minimum requirements for the floor material of the polyurethane mortar system. If the above standards do not meet the above standards, please remedy or contact the technical support of Shandong Dushili in the selection of primer.
Grassroots treatment
1. Clean the surface, clean up the dust debris, and use the cleaner to remove the surface oil if necessary;
2. Repair ground defects, such as heavy oil pollution areas, scratches, construction seams and cracks to repair;
3. Pre -coating base surface passes the grinding treatment of the shot blasting machine or grinding machine, except for the surface floating slurry, dust and other debris, and provides a solid and rough surface to the surface;
4. Opening anchor grooves, conventional use of 80cm -100cm to see square grooves, 5mm wide and depth of each as conventional cut, and special seam treatment at the key locations such as the door, the edge of the wall, the load -bearing column, the equipment base, and the sink.
Construction of bottom coating
1. Purpose: ① Let the surface layer be better attached to the grassroots; ② completely close the air in the grassroots (prevent pinholes);
③ Reduce the impact of the gap between the grassroots and the opposite layer.
2. Step: ① Shake the group A and pour in the stirring bucket, then add the part of the D component for 30 seconds to evenly, then add the B component to stir for 10-30 seconds, add the C, stir in the stirring state 1- 1- 1- 1- 1- 2 minutes to uniform. The uniform state is a viscous mortar with color uniform.
② The tuned material is evenly coated with a sawtooth knife evenly on the processed grass level.
③ Combined with the construction environment, according to different seasons and temperatures, when the materials that are scraped in the last batch have slightly viscosity, scrape it with a flat scraper again, which has achieved a better closed effect.
3. Suggested dosage: 2kg/㎡.
Construction of surface layer of water -based polyurethane mortar system
The following elements are mainly considered by the construction of the surface layer:
1. Operation time: When the ground temperature is 20 ° C, the operation time is 10 minutes.
2. Stirring time: first shake the group A and pour into the stirring barrel, then add the part of the D component for 30 seconds to evenly, then add the B component to stir for 10-30 seconds, add the C component in the stirring state 1- 1- 1- 1- 1- 1- 2 minutes to uniform. The uniform state is a viscous mortar with color uniform.
3. Construction continuity: According to different seasons and temperatures, keep all aspects of the entire construction process and synchronize the entire construction process. It is recommended not to be too long (stir-transport-paving-bubbles) to avoid excessive solidification of materials. Unused, affecting the performance of the overall material.
4. Coating tools: It is recommended to use jagged knife or fine -toothed rake, and bubble drums. After the slurry is matched with the ground (not to be stored in the mixing barrel), the sawtooth knife or the tooth rake is scraped evenly. After the scraping is finished, follow the nail shoes with a bubble drum and batch scraping direction.
5. The recommended dosage: 2kg/㎡ per millimeter thick.
Technical indicator
serial number | test items | detection method | judgment value | Test results | Single item judgment | |
1 | status in the container | JC/T 2327-2015 (2017) | The liquid component is mixed after stirring; | The liquid components are mixed after stirring; | Qualification | |
2 | Appearance | The surface is flat, no cracks, and the color is uniform | The surface is flat, no cracks, and the color is uniform | Qualification | ||
3 | Operating time | ≥20 | 30 | Qualification | ||
4 | flow, mm | jc/t 985-2005 | ≥130 | 152 | Qualification | |
5 | 24h pressure resistance, MPA | GB/T 17671-2021 | ≥20 | 35 | Qualification | |
6 | 7D pressure resistance, MPA | ≥40 | 43 | Qualification | ||
7 | 7D anti -folding strength, MPA | ≥10 | 16 | Qualification | ||
8 | 7D stretching and bonding strength | GB/T 22374-2008 | ≥2.0 | 5.1 | Qualification | |
9 | Anti -slip (dry friction coefficient) | GB/T 4100-2006 | ≥0.6 | 0.6 | Qualification | |
10 | wear resistance (500G/100R), G | GB/T 1768-2006 | ≤0.15 | 0.04 | Qualification | |
11 | impact resistance (1kg, 200cm) | JC/T 2327-2015 (2017) | no crack, no peeling | no crack, no peeling | Qualification | |
12 | Water resistance (168H) | No foaming, no peeling, no cracks, no discoloration | No foaming, no peeling, no cracks, no discoloration | Qualification | ||
13 | alkali resistance (20%sodium hydroxide, 72H) | No foam, no peeling, no cracks, allowing slight discoloration | No foaming, no peeling, no cracks, no discoloration | Qualification | ||
14 | Oil resistance (120#solvent oil, 72H) | No foam, no peeling, no cracks, allowing slight discoloration | No foaming, no peeling, no cracks, no discoloration | Qualification | ||
15 | saline resistance (3%sodium chloride, 7D) | No foam, no peeling, no cracks, allowing slight discoloration | No foaming, no peeling, no cracks, no discoloration | Qualification | ||
16 | acid resistance (48h) \ | 10%sulfuric acid | No foam, no peeling, no cracks, allowing slight discoloration | No foaming, no peeling, no cracks, no discoloration | Qualification | |
10%citric acid | No foam, no peeling, no cracks, allowing slight discoloration | No foaming, no peeling, no cracks, no discoloration | Qualification | |||
10%lactic acid | No foam, no peeling, no cracks, allowing slight discoloration | No foaming, no peeling, no cracks, no discoloration | Qualification | |||
10%acetic acid | No foam, no peeling, no cracks | No foam, no peeling, no cracks | Qualification | |||
17 | Volatile organic compound (VOC), G/L | GB 18582-2008 | ≤20 | No detection | Qualification | |
18 | Benzene, toluene, ethylene, mate, mg/kg | ≤30 | No detection | Qualification | ||
19 | free formaldehyde, mg/kg | ≤30 | 7 | Qualification | ||
20 | soluble heavy metal | lead PB |
GB 18582-2008 |
≤30 | Unobed | Qualification |
cadmium CD | ≤30 | Unobed | Qualification | |||
chromium CR | ≤30 | Unobed | Qualification | |||
mercury hg | ≤10 | Unobed | Qualification |
PRODUCTION BASE
The company is committed to product technological innovation and building new platforms to improve its capabilities. In order to continuously improve its core competitiveness in the market and meet new market demands, Des-Lead has established a research and development center. The company has more than 10 professional R&D teams in the fields of flooring, sports, waterproofing and anti-corrosion, and polyurea. It continues to research products that better meet market needs, pays attention to ecological construction, and actively tries environmental protection technology. It has maintained vigorous vitality and abundant market vitality in the fierce market changes and market competition.

PRODUCTION LINE
Des-Lead has its own independent production base and has established a world-leading fully automatic assembly line with a comprehensive daily output of 100 tons and an annual service site area of more than 10 million square meters. The strict quality management system ensures the quality and efficiency of Des-Lead products.

RELATED PRODUCTS
ONLINE MESSAGE